纖維增強復合材料在3D打印領域的應用日益廣泛,涵蓋航空航天、電子、紡織和彈道等行業。3D打印技術降低了成本,縮短了生產周期,為這些領域的產品設計提供了更大的靈活性和創新空間。例如,在航空航天領域,該技術已用于制造巨型衛星燃料箱;在電子工業,推動了柔性電子產品的創新;紡織工業則利用該技術打印智能紡織品;彈道工業則提高了生產效率,實現了復雜設計。這些變革預示著未來技術發展的巨大潛力。3D打印技術可創造復雜幾何形狀。借助3D打印機器人與先進工藝,我們能夠直接制造出大型集成部件,無需繁瑣的組裝過程,如圖1(a-d)所示。這些加工上的優勢確保了復合材料在與替代EMIS材料的競爭中,依然保持著成本競爭力。此外,3D打印技術還具備材料選擇的靈活性,能夠兼容多種基質材料。這些基質材料涵蓋了廣泛的熱塑性塑料,包括PLA、ABS、PC、PP、PS、PA以及高性能的PEEK等,為制備多功能且易于加工的屏蔽材料提供了豐富的選擇。
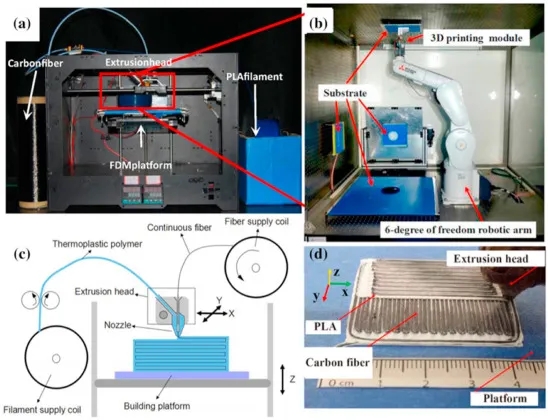
圖1 (a) FDM 3D打印機 (b) 3D打印機器人 (c) 3D打印過程的流程圖(d) 打印樣品
1、航空航天工業
航空航天工業(圖2(a-c))極大地受益于3D打印技術的發展。該技術能夠迅速制造具有復雜工程幾何形狀的產品,成為航空航天部門的理想選擇。這些產品憑借其低產量、卓越的質量、輕盈的重量以及耐高溫等顯著優勢,贏得了業界的青睞。
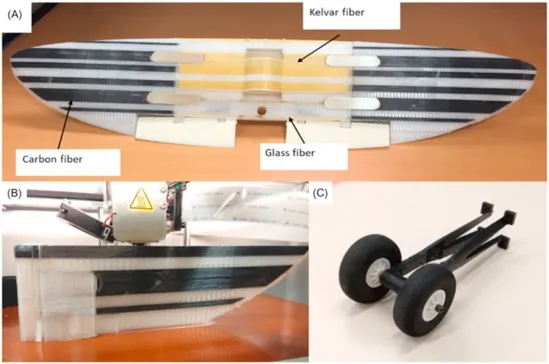
圖2 (A) 由凱夫拉、碳纖維和玻璃纖維增強的熱塑性塑料制成的機翼;(B)無人機(UAV)機翼上無縫連接的碳纖維層壓;(C) 通過3D打印技術制造的無人機起落架
通過將連續纖維融入3D打印流程,能夠創造出高強度重量比的輕質結構,這一特性不僅適用于航空航天領域,也廣泛應用于汽車行業。納米復合材料的加入進一步提升了復合材料的電導率和熱導率,同時改善了其分層性能。然而,CFRC(碳纖維增強復合材料)在航空航天工業中以其卓越的高剛度和比強度脫穎而出。采用3D打印技術制造CFRC已成為制造復雜復合材料結構的一種高效方法?;厮葜?014年,美國宇航局攜手軌道上制造公司,在國際空間站上成功完成了首次太空3D打印研究,期間生產了超過20個純PLA樣本(如圖3(a & b)所示)。時至2020年,西安交通大學與中國空間技術研究院的研究團隊攜手,在宇宙飛船上成功實施了中國的首次3D打印實驗(如圖3(c)所示)。受NASA蜘蛛模型構想的啟發(如圖3(d)所示),設想中的太空機器人將運用連續碳纖維增強的PEEK復合材料,構建一座壯觀的螺旋結構。此外,蘇黎世聯邦理工學院的CMASLab團隊更是創新性地設計并測試了一種由3D打印CFRCs制成的變形無人機(如圖3(e)所示),該無人機僅憑變形控制面便能實現滾動、俯仰和偏航的精準操控。值得注意的是,高真空環境、極端溫差以及強輻射等,僅是3D打印技術在航空航天工業中必須克服的眾多嚴苛條件中的一部分。
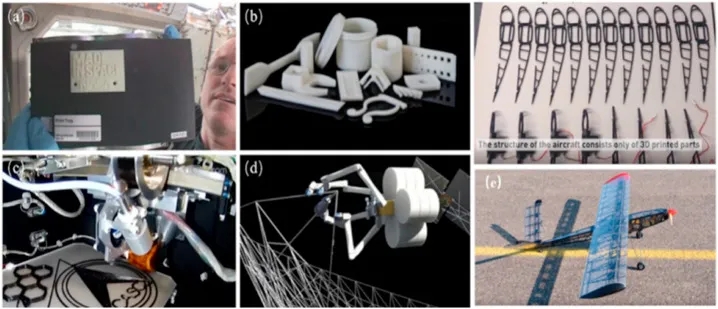
圖3 (a-b)3D打印制品 (c)用連續碳纖維增強的PLA復合材料(d)用于構建巨大結構的Spider Fab (e)使用CFRCs進行3D打印的無人機結構件MAS(多層裝甲系統)是一種卓越的防御裝置。該系統巧妙地融合了多種先進的合成材料,特別是凱夫拉纖維與鋁合金的運用。在探索MAS及其相關領域的潛在應用時,NFRPC無疑是新材料中最引人注目的亮點之一。作為多智能體系統架構中不可或缺的第二層組件,NFRPC展現了其獨特的價值。研究團隊對不同濃度的圖形纖維進行了深入研究。實驗結果表明,當纖維體積分數達到30%時,所制成的聚酯復合材料在承受沖擊后,不僅保持了出色的結構完整性,還展現了卓越的能量吸收性能,使其成為凱夫拉爾纖維的理想替代品。
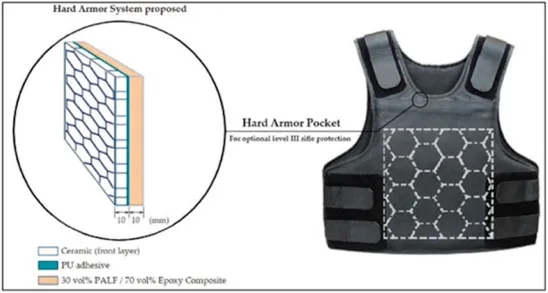
圖4清晰呈現了彈道硬裝甲系統的基本構造示意圖,深刻揭示了這一前沿防御技術的核心要素。分析棕櫚纖維基NFRPC的彈道性能特征,明確指出復合材料中棕櫚纖維的體積占比范圍為10%至50%。在彈道學評估環節中,采用7.62毫米口徑彈藥作為基準測試,以穿透深度為關鍵衡量標準,嚴格驗證系統是否符合NIJ標準0101.06的規范需求。試驗結果顯示,表層覆蓋木薯纖維復合材料的樣本展現出卓越的防護效能,強有力地證明了環保型木薯纖維在防護體系中的可行性與優越性。彈道納米復合材料領域正成為科研熱點。通過將納米粘土融入基質體系,成功制備出性能顯著提升的玻璃-環氧納米復合材料。此類材料在遭遇沖擊時,基質紗線的拉伸失效與分層現象有效耗散了沖擊能量。引入納米顆粒不僅增強了纖維與基質間的粘附力,還優化了纖維基質的界面結合性能。特別地,我們還對氧化鋁制成的3D打印鎧裝鋼板進行了有效性評估。通過PSD板與DIW板的彈道性能對比,發現DIW板在抗沖擊性、硬度及彎曲強度等方面均優于PSD板,這主要歸因于其較小的晶粒尺寸帶來的韌性提升。
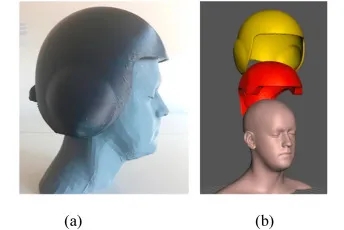
展望未來技術突破后3D打印在創造個性化盔甲方面的獨特優勢。特別是在材料浪費和人力投入方面,3D打印技術展現出顯著優勢,更適合于定制化、小批量生產的場景。本概念項目強調了利用3D打印技術輕松創建與用戶完美貼合的(硬)防彈衣的潛力,并展示了如何通過簡單方式增強產品的新(復雜)功能,無需大量投資于新機械設備的研發。3D打印技術在紡織品領域展現出了多元化的應用模式,其卓越的精密設計與細節處理能力,可能使其相較于傳統制造方法具備顯著優勢。天然纖維,憑借其獨特的粗糙質感,成為了3D打印材料的理想材料,這一選擇深植于它們各自獨特的物理屬性之中。研究表明,樣品的毛感、粗糙度、疏水性和潤濕性等特性,均與打印漿料的粘附性能緊密相關。得益于天然纖維的親水性,打印漿料能夠輕松滲透織物并實現牢固結合。特別是羊毛纖維,其表面的粗糙性更是顯著增強了粘附效果。在紡織制造領域引入或實施3DP技術的核心目標,應聚焦于模擬并優化紡織品的關鍵品質特征,包括但不限于柔軟觸感、柔韌性能、強度水平及孔隙度等核心要素。通過運用三維編織、針織或織造技術,我們能夠顯著提升織物的厚度,使螺旋線或纖維在厚度軸上實現有序排列,從而構建出獨特的三維局部結構。這些技術在三維空間內所展現出的“3D”特征尤為顯著。盡管這些創新技術展現出了塑造復雜三維形態的巨大潛力,但目前尚無一技術能夠獨當一面,直接應用于服裝的規模化生產。然而,這也為時裝設計師與功能性可穿戴設備設計師帶來了前所未有的機遇。他們得以擺脫針織、編織等傳統生產方式的束縛,從3D打印技術賦予的完全定制化生產能力中汲取靈感,創造出前所未有的設計作品。
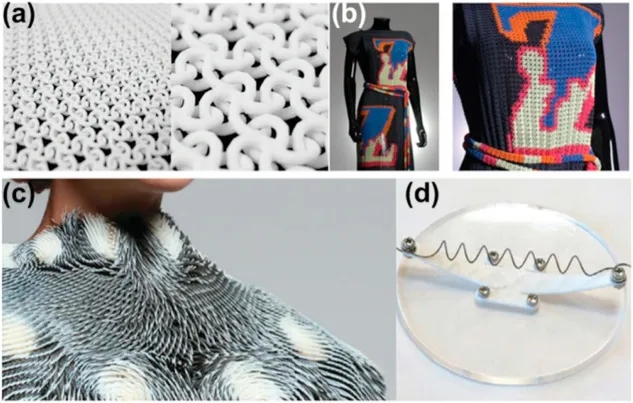
圖6展示了利用不同硬件或紡織品材料通過3D打印技術制成的時尚服飾作品。具體而言,圖6a與b展示了采用PA(聚酰胺)與SLS(選擇性激光燒結)技術制成的印刷時裝作品,其尺寸精細為(9.5×9.5×3.6mm)。此外,圖6c與d揭示了3D打印技術在流體可穿戴設備上的應用,這些設備具備清晰的區域劃分,能夠產生多樣化的聲音與光影效果;通過將熱塑性聚氨酯(TPU)與SLS技術結合,創造出細密的編織線,模擬出蕾絲般的紋理,用于裙裝設計;更有甚者,在多材料3D打印技術(精度高達16μm)中加入形狀記憶合金(SMA),開發出能夠響應人體動作乃至目光注視的柔性網格結構。導電復合材料是指那些具備卓越電導率特性的復合材料。當適量的聚合物樹脂與導電填料,特別是像石墨烯這樣的碳基化合物相融合時,便能打造出導電復合材料。隨著填料含量的遞增,復合材料內的導電粒子間開始相互作用,構建出一條連續的導電通道,使得電子得以自由流通。此類材料不僅耐腐蝕、質輕,還能根據特定需求進行形狀設計,因此,在某些應用場景下,它們能夠有效替代傳統金屬。導電復合材料的用途廣泛,涵蓋了涂層、電池、傳感器、電極以及電磁干擾屏蔽材料等多個領域。隨著3D打印技術的飛速發展及其在研究、技術和工業領域的日益普及,制造商們正逐漸認識到這一技術所帶來的巨大潛力。特別是熔融沉積成型(FDM)3D打印技術,它使得3D電極的制造既經濟又高效,且其結構與表面積相較于銅、鋁和碳電極展現出更高的靈活性。該打印技術全自動化且精準度高,能夠在短短30分鐘內完成8個電極的打印工作。圖7所展示的新型打印納米復合材料中,MEMS、芯片實驗室、工程材料、微流體、組織工程、微電子以及光子學等領域均展現出了其顯著的價值。針對用于流體傳感和電磁干擾(EMI)屏蔽的2D及3D結構,Serizawa等人報告了通過SC-3D打印技術生產的高導電性納米復合組件(電導率高達5000 Sm-1)的研究成果。他們利用球磨機將20%的聚乳酸(PLA)與碳納米管進行混合,并發現盡管通過打印機的小噴嘴擠出高達40%納米管負載的復合材料存在困難,但打印出的納米復合材料在作為3D支架以阻斷電磁干擾方面,其性能明顯優于熱壓固體復合材料。
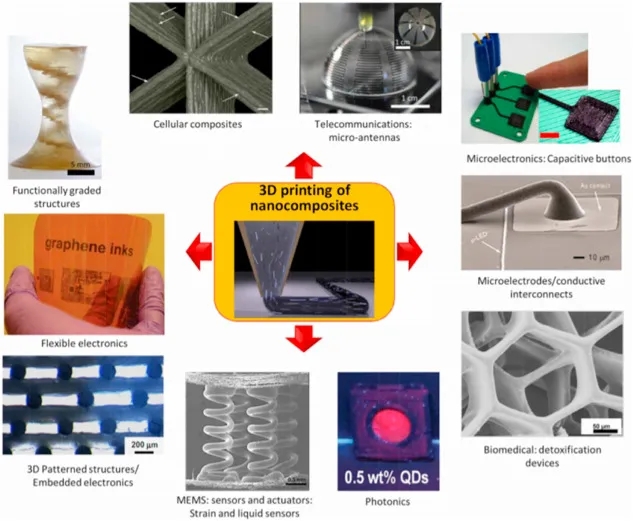
圖7 微流體、微機電系統(MEMS)、工程復合材料、微電子和電信五個領域以各種3D打印技術產生的三維納米復合材料宏觀和微觀結構圖此外,羅馬尼亞布加勒斯特理工大學的研究小組成功開發并測試了一種創新的三維、多層石墨烯生物傳感器。在設計過程中,科研人員特別重視了傳感器本身及其與界面的兼容性,這對于實現高靈敏度的葡萄糖檢測至關重要。研究人員巧妙地將兩親性吡咯單體與葡萄糖氧化酶結合,并吸附于鉑電極上,通過氧化聚合反應,制備出了先進的葡萄糖生物傳感器。然而,這類傳感器在遇到內源性物質(如抗壞血酸和尿酸鹽)和外源性物質(如撲熱息痛)時,容易受到顯著干擾,尤其是在0.5 V電壓下,基于過氧化氫電氧化和形狀改變效應的傳感器體系中。A comprehensive exploration of 3D printing with fiber-reinforced composites in aerospace, automotive, medical, and consumer industries